Validated designs for Covid-19 relief efforts.

Download, print, support your community
If you are a manufacturer ready to make 500+ units a week, or a hobbyist making PPE for friends and family - these design files are easily printed on most rapid manufacturing devices. OU Health Sciences Center doctors, researchers, and front-line health care professionals have tested these designs and determined then essential and effective as part of a Covid-19 safety protocol.
Manufacturing instructions and design files are listed for each, below.
Before producing any of these designs for your local health care professionals or first responders, please confirm their needs and where they are collecting items.
Fabrication Specifications
LULZBOT TAZ 6 / MINI 2 KEY SETTINGS
Layer Height: 0.18 mm
Initial Layer Height: 0.25 mm
Line Width: 0.5 mm
Wall Thickness: 1.04 mm
Wall Line Count: 2
Infill Density: 25%
Top/Bottom Thickness: 1 mm
Extruder Temperature: 215 C
Print Speed: 80 mm/s
Infill Speed: 80 mm/s
Wall Speed: 40 mm/s
Travel Speed: 175 mm/s
Lulzbot TAZ 6 Tool Head: Single Extruder Tool Head v2.1 (.50mm Nozzle)
Lulzbot Mini 2 Tool Head: E3D Titan Aero SE (.50mm Nozzle)
Printer / Filament Brand Used: TAZ 6 / Gizmo Dorks PLA
Printer / Filament Brand Used For Interface Gasket: Mini 2 / Ninjatek NinjaFlex TPU
MAKERBOT KEY SETTINGS
Layer Height: 0.2 mm
Line Width: 0.5 mm
Wall Width: 0.5 mm
Wall Line Count: 4
Infill Density: 100%
Top/Bottom Thickness: 0.8 mm
Extruder Temperature: 215-230C
Print Speed: 120 mm/s
Infill Speed: 90 mm/s
Travel Speed: 150 mm/s
Filament Brand Used During Prototyping: Makerbot Filament PLA
Filament Brand Used For Interface Gasket: n/a
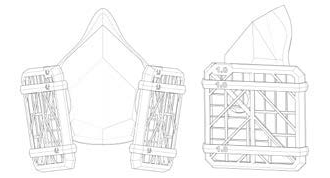
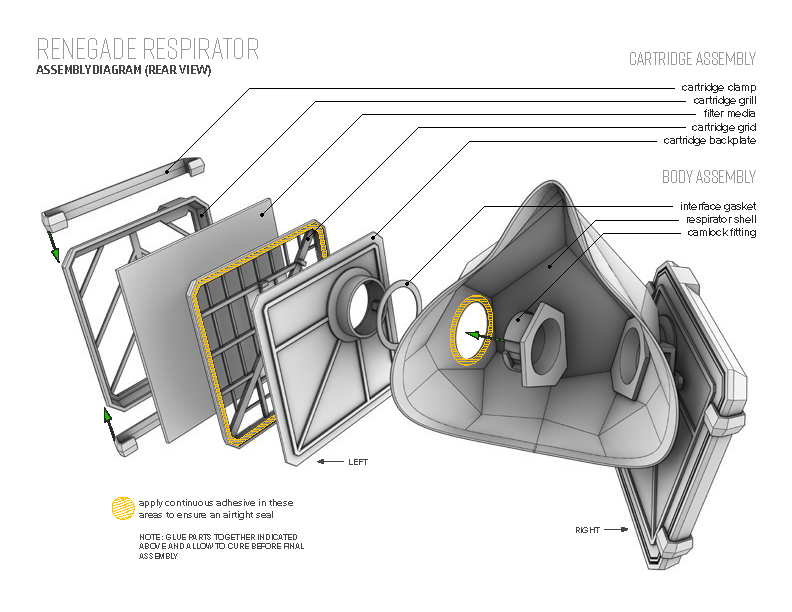
Heat Molding & Fit Customization
STEP 1:
Clean the mask after printing, remove burrs and strings. Use a 150-grit sandpaper to sand the inside surface that you expect to contact your face. The smoother the better. Use a cloth wetted with acetone to further smooth the sanded surface if desired.
STEP 2:
Install the camlock valves with silicone or similar sealant/adhesive
o Apply the valves before heat molding to better retain mask shape
o Allow to fully cure before heat molding
STEP 3:
Place the mask shell in an oven preheated to 80°C (176°F) for 3 minutes. Place the mask open side up, on a folded paper towel placed in a baking dish to prevent the metal grill from melting the shell. Set up a mirror or camera phone on selfie mode nearby the oven to use during Step 04.
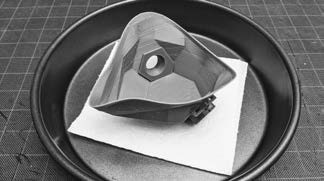
STEP 4:
Remove the mask shell from oven and gently press the mask to your face with a slight pivoting motion. Lightly anchor below your chin then pivot to contact the rest of your face. Use your fingers to gently press the mask against your nose bridge and cheek bones. Use the mirror or phone on selfie mode to guide your actions.
Shape your hand position as if yelling across a field; use your index fingers and thumbs to gently contour the soft plastic to your face. The mask hardens within seconds even though it still feels warm.
Inspect the fit in the mirror and note how well it seats on your nose bridge and upper cheeks. These are the most likely areas to leak.
STEP 5:
Repeat the heat molding process, this time press a little bit harder on the sides of your nose and upper cheeks. Do not over do it! Do not press your fingers towards each other, that will make a crease on the top of your nose bridge and cause a leak. Try to apply even pressure with your whole finger, not just the fingertips
STEP 6:
A gasket may be added around the edge of the mask to improve comfort and fit.
Download:
The design files for this product will be made available at a later date. For now, you can download a design PDF with the information and instructions outlineded here.
Design Specifications Renegade Design Files
By downloading these files you agree to the terms of the University’s COVID Use License
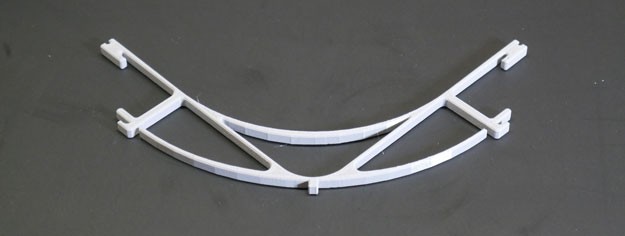
Machines Required:
- 3D printer
- Laser cutter
- Or CNC machine
Material:
PLA, PETG, HDPE, ABS
Considerations:
This face shield frame, designed by Nathan Herring, tech lead, Tom Love Innovation Hub, can be 3D printed, laser cut, or CNC machined. It works with a simple hole-punched 8.5x11 piece of transparency paper - a readily accessible material through amazon or other retailers.
If cutting the frame on a laser, use with HDPE or ABS. Even though the laser will slightly ablate the edges of the materials, the slightly raised edge aids with comfort. Avoid using acrylic, as its edges are sharp and uncomfortable, it's also brittle and could shatter when flexed. Each unit will need some scrubbing out of the laser though, to remove soot and particulate.
When 3D printing, we recommend PLA or PETG, because of ease of access.
This part can be machined on any CNC router, though special care must be taken to hold the material down with the number of cuts and pieces in the design.
Herring Face Shield Assembly
Assembly:
This design is simple, needing only the frame, shield, and strap - with optional forehead band for comfort.
After producing the frame, simply attach a standard 3-hole punched transparency sheet across the three tabs on the front of the frame, and then stretch a silicone headband around the back to fit. If more coverage is desired above the frame, cut a transparency in half long-ways, hole punch it, and add it upside-down.
This frame can be sanitized for multiple uses. This is dependent on the preferences of the practitioner, and availability of supplies.
Download
We encourage you to download these designs and produce them for your local hospital or healthcare organization after confirming their need:
By downloading these files you agree to the terms of the University’s COVID Use License
Additional Files
These files improve upon the designs fit and durability, but require laser cutting to produce. The Comfort Band is cut from any thin plastic, or can be 3D printed as thin as you dare on your machine. The silicone headband is cut from inexpensive silicone baking mats. Both will require some cleanup coming out of the laser:
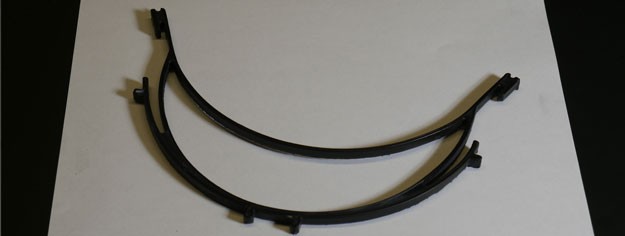
Machines Required:
- 3D printer
- Laser cutter
- Or CNC machine
Material:
PLA, PETG, HDPE, ABS
Considerations:
This face shield frame, designed by Tyler Thibodeau, senior tech lead, Tom Love Innovation Hub, can 3D printed, laser cut, or CNC machined. It works with a simple twice-hole-punched 8.5x11 piece of transparency paper using a convenient spacer for flipping and aligning the sheet - which is still a readily accessible material through amazon or other retailers.
If cutting the frame on a laser, use with HDPE or ABS. Even though the laser will slightly ablate the edges of the materials, the slightly raised edge aids with comfort. Avoid using acrylic, as its edges are sharp and uncomfortable, it's also brittle and could shatter when flexed. Each unit will need some scrubbing out of the laser though, to remove soot and particulate.
When 3D printing, we recommend PLA or PETG, because of ease of access.
This part can be machined on any CNC router, though special care must be taken to hold the material down with the number of cuts and pieces in the design.
Thibodeau Face Shield Assembly
Assembly:
Simple design including only frame, brace, shield, and strap - with optional forehead band for comfort. The lower brace helps with rigidity.
After producing the frame, you'll need to hole punch a standard transparency sheet twice. Use the available spacer file to align the sheet in a standard hole punch, then flip the sheet over and punch it again. Stretch the transparency sheet across the four tabs on the front of the frame. You can place the forehead comfort band as well, then stretch a silicone headband around the back to fit. If more coverage is desired above the frame, cut a transparency in half long-ways, hole punch it the same as before, and add it upside-down.
This frame can be sanitized for multiple uses. This is dependent on the preferences of the practitioner, and availability of supplies.
Download:
We encourage you to download these designs and produce them for your local hospital or healthcare organization after confirming their need:
By downloading these files you agree to the terms of the University’s COVID Use License
Additional Files
These files improve upon the designs fit and durability, but require laser cutting to produce. The Comfort Band is cut from any thin plastic, or can be 3D printed as thin as you dare on your machine. The silicone headband is cut from inexpensive silicone baking mats. Both will require some cleanup coming out of the laser:
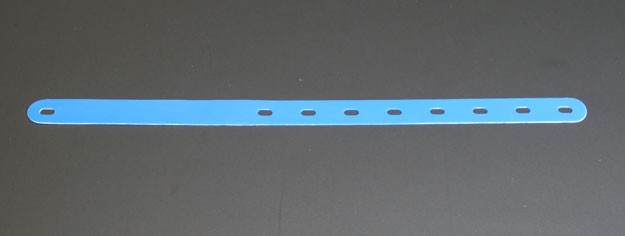
Machine:
Laser cutter
Material:
Silicone rubber, ~1mm thickness
This silicone strap, designed by Tyler Thibodeau, senior tech lead, Tom Love Innovation Hub, will fit virtually all of the open source face shield designs available - certainly all available on this website. The silicone is thin enough to stretch, and has simple holes for adjustable sizing.
This simple design has received more positive reaction from our healthcare professionals than any of the other designs because of its comfort. The silicone can also be cleaned and reused.
By downloading these files you agree to the terms of the University’s COVID Use License
Cleaning Process
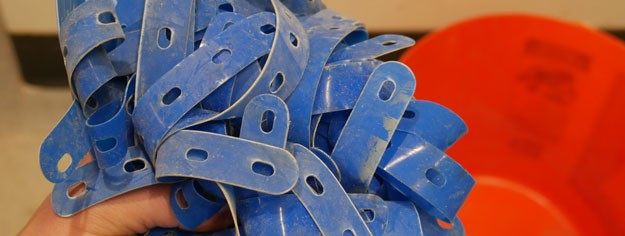
The straps will likely be covered in soot and ash from the cutting process. Some of the small holes may re-melt and cool together. These need to be cleaned before delivery.
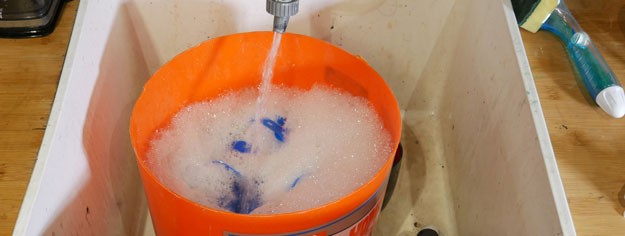
We soaked our prototypes in 5-gallon buckets with a healthy amount of regular dish soap and hot water. Then, we used a length of scrap wood to stir and agitate the straps for several minutes.
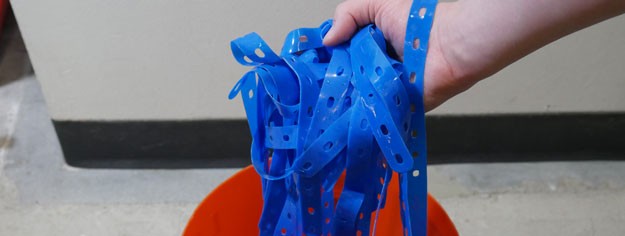
Rinse the straps clean of soap and then hang to dry. These straps pair well with many commercial face shields including the designs listed, here.
Disclaimer:
The Board of Regents of the University of Oklahoma (“University”) makes no representation or warranty of any kind with respect to the 3D printing design for a “3D Printed Face Shield” (“Design”), whether express or implied, including any representation or warranty relating to the compliance of any 3D printed part based on such Design with any specific regulation, any warranty of merchantability, fitness for a particular purpose, or non-infringement of any patent or other proprietary right.
The Design should not be considered Personal Protective Equipment or “PPE” because its capability to provide protection is unknown. Caution should be exercised when considering the use of the Design. The Design is not intended to be a suitable replacement for N-95 or other surgical masks for healthcare workers, nor does it eliminate the risk of contracting or exposure of others to any disease or infection. The Design and manufacturing of this “3D Printed Face Shield” is not regulated by the U.S. Food & Drug Administration or the U.S. Centers for Disease Control and Prevention (CDC), nor has it been evaluated or approved by The National Institute for Occupational Safety and Health (NIOSH) or any other regulatory authority.
The individual, group, organization, or any other entity downloading the Design (“User”) acknowledges that User downloads and uses the Design at User’s own free will and own initiative and is aware that there are certain risks associated with using the 3D printed parts based on such Design, including but not limited to, injury to the body,general health, and well-being, death, and/or property damage. User hereby voluntarily assumes all risks associatedwith downloading and using the Design, including the suitability and compliance with any applicable regulations.
The University shall not be liable for any claims, demands, damages or injuries, including but not limited to, property damage, bodily injury, death, indirect, special or consequential damages, arising out of or in connection with User’s downloading, manufacture, commercialization, and any other use of the Design.